Air Tightness Testing
There is a requirement under the Building Regulations to complete an air leakage test (also known as a blower door or air permeability test) on your home on practical completion.
The results of the test are then provided to your architect or engineer for Compliance purposes and used in the final BER calculation and the results of the test are accounted for in the overall BER.
The purpose of undertaking the air leakage test is of course to prove compliance with Building Regulations.
You are obliged to undertake one test only but if you are building a very airtight house with a mechanical ventilation system installed it might make sense in conjunction with advice from your designer/builder to do 2 tests.
The first would be done at first fix stage once the initial airtight layer is installed to determine how good it is and to benchmark it against your design specification.
It is very cost effective to do an air leakage test at first fix stage as the final layers of the house are not in place so finding and fixing the leaks are easy to do and inexpensive.
If your compliance or the functionality of installed mechanical ventilation systems requires a good outcome (e.g. ≤ 3 air changes per hour at 50 Pascal pressure differential) then it makes sense to do two tests.
If the house does not perform as designed and particularly where a mechanical ventilation system has been installed it can never operate efficiently – wasting your money.
When we undertake an air leakage test it is done to the highest
standards (I.S. EN ISO 9972:2015) and in accordance with NSAI specifications & INAB Certificaition.
2eva staff undertaking air leakage tests are highly trained, experienced and will work with you to maximise your test outcome.
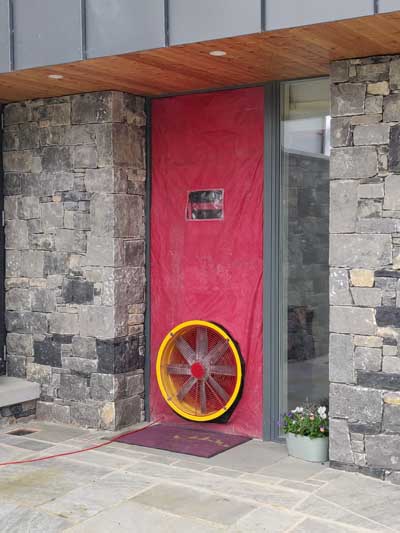
As a builder/developer you have an obligation under either the 2011 or 2019 Building Regulations to complete tests to a defined minimum standard. This will depend on whether the project had Planning Applied for before or after 31st October, 2019.
This will have an impact on two key elements of your obligations – the first being the maximum upper limit you have to test to:
≤ 7 m³ h m² under the 2011 Building Regulations
≤ 5 m³ h m² under the 2019 nZEB/Building Regulations
The second is the number of air leakage tests that have to be performed on the project. If dwellings are being completed under the 2011 Building Regulations then they are subject to the minimums set out in the Sample Regime that we can explain to you but if under the 2019 nZEB/Building Regulations then each and every dwelling has to be tested.
We have vast experience of working closely with our business partners to ensure that we maximise the outcomes on site when undertaking air leakage testing. Our experienced colleagues work with your team before we ever get to site to discuss how to prepare the building and the best methodology to employ.
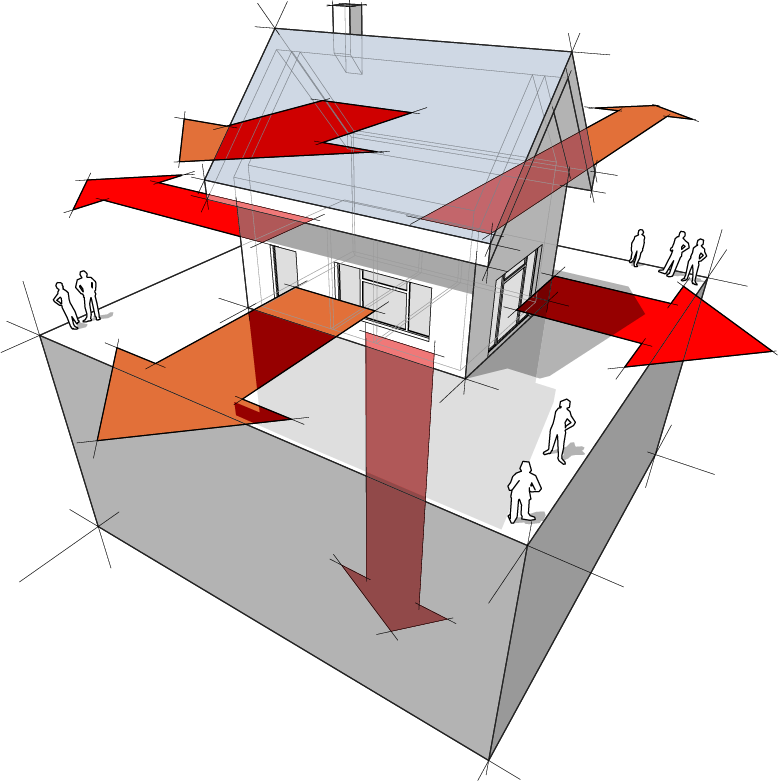
We often visit site prior to the first set of tests to meet the air tightness champion and walk the buildings to be tested to identify visual flaws prior to testing. This is a win-win situation for the client as well as us, as it means that the actual process of testing works better and ensures better outcomes.
As we are testing under the demanding NSAI Standards we will test the building using both positive and negative pressure to a minimum of 50Pa pressure difference.
The outcomes will be reported for both the air changes per hour rate and the one required by the Building Regulations – air permeability rate.
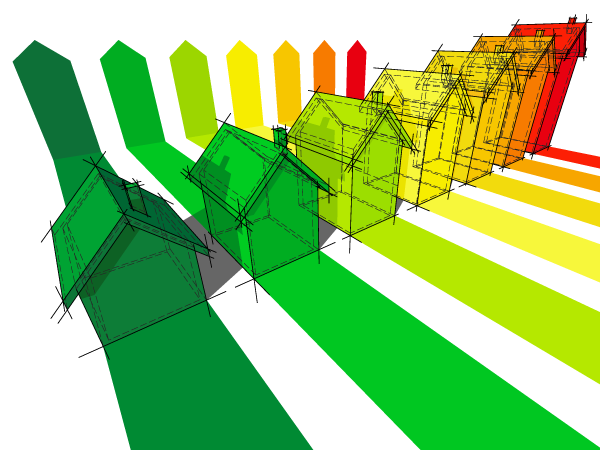
Critically however, if one of the critical factors of your the DEAP calculation for your BER is dependant on an input value lower than the backstop value of 7 m³/hr/m² then a test must be performed on each dwelling proving the input value.
The n50 is the air change rate at and is expressed in air changes per hour (ac/h). It is the relationship between the total volume of air in m³ and how often leaks in the
building envelope allow the air to exchange at 50 Pascals air pressure difference.
The q50 is the air permeability rate and is expressed as m³ h m². It is an expression of the amount of air leaked from the dwelling in relation to the total exposed surface area
of the building (i.e. the ground floor, all exposed ceilings and all external walls [including party walls/floors in the case of semi-detached, terraced or apartment dwellings) at 50 Pascals pressure.
All tests we undertake are done to the highest standards (I.S. EN ISO 9972:2015) and in accordance with NSAI specifications.
The results of the air leakage test on each dwelling will be provided in a report in accordance with NSAI standards and the outcome can be inputted into the final DEAP calculation to verify Compliance with 2011 Building Regulations or 2019 nZEB/Building Regulations.
Number of Pressure Tests per Dwelling Type
|
|
---|---|
Number of Units
|
Number of Tests |
1 to 4 | 1 Test |
Greater than 4, but less than or equal to 40 | 2 Tests |
Greater than 40, but less than or equal to 100 | At least 5% |
More than 100 (a) When the first 5 tests achieve the design air permeability |
At least 2% (for dwellings in excess of first 100 units) |
(b) Where 1 or more of first 5 Tests to not achieve the design air permeability
|
At least 5% of units, until 5 successful consecutive tests are achieved, 2% afterward
|
Types of Air Tightness Test
Air leakage tests happen when a pressure difference of typically +/- 50 Pascals (Pa) is generated between the inside and outside of the building in comparison to natural air pressure using a fan suitable for this purpose. This can be either under pressure (i.e. air is pulled out of the building) or overpressure (i.e. air is blown into the building) and ideally a combination test of both.
Air tightness testing equipment can be used in several ways.
The standard air tightness or blower door test requires that a single fan get set up in a doorway into an expandable frame that fills the doorway. Onto the frame is mounted a canvas type membrane or cloth with a hole in it. The testing fan is then fit into the frame/cover and is operated using bespoke software generating positive and negative pressure as required. A single fan will normally be enough for a single dwelling.
The process is operated by a skilled, trained and experienced operative. The operative will have the desired mix of onsite practical experience as well as the training to both operate the equipment and advise clients of the location and severity of leaks.
Where suitable as the picture to the right here shows we can use smoke to demonstrate the location of leaks – in this case via a window slider.
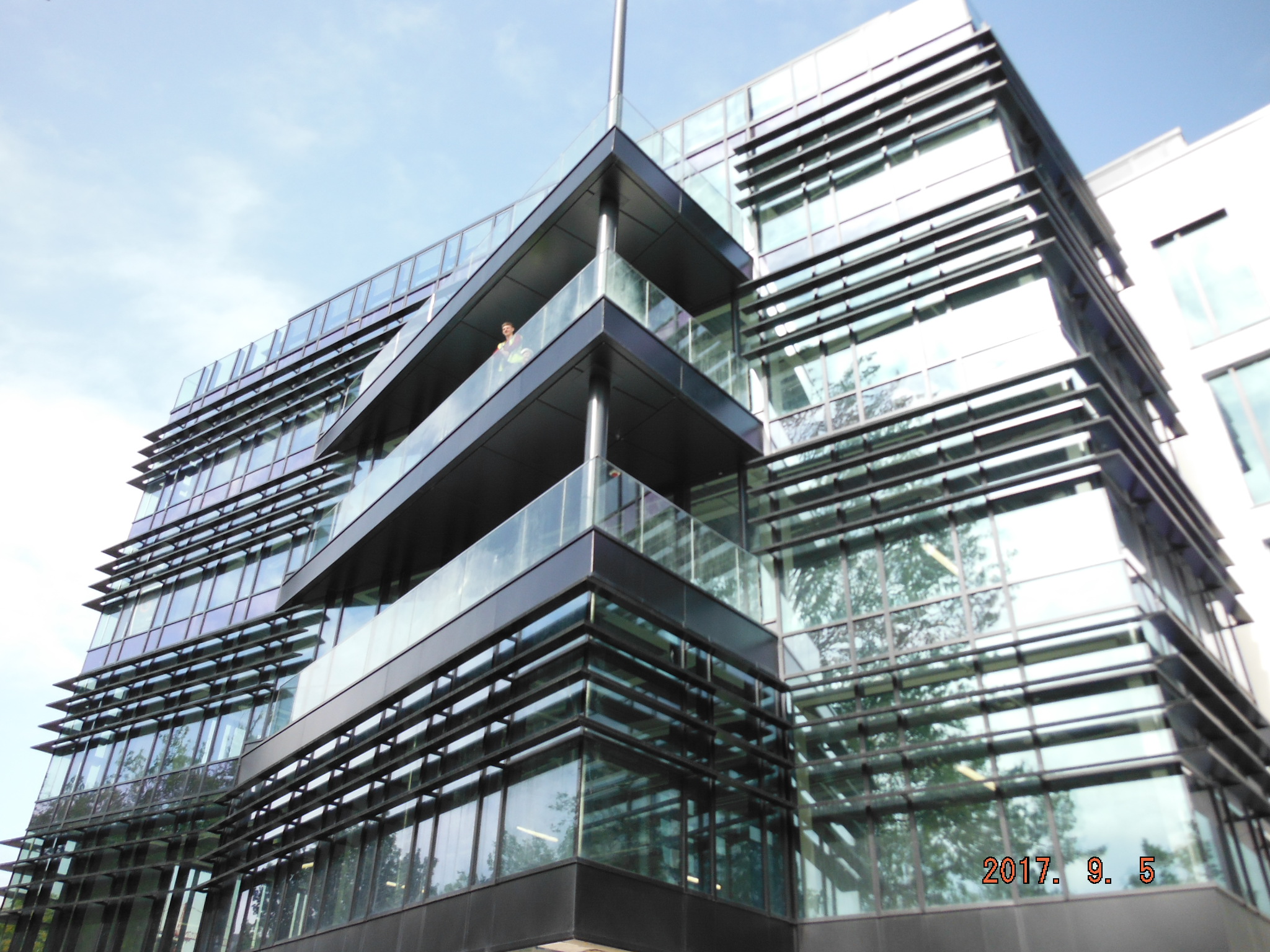
This ideal blend of talent and experience helps to maximise the air tightness test outcome.
For much larger or leakier buildings, the fans can be stacked and the combined air moving effort be used to create the same 50 Pascal pressure difference as for a domestic dwelling. The principle is the same but you match the amount of collective fan power to the expected leakage and the design target for the building.
The pre site work is more intensive as the job needs to be scrutinised in detail and the scale and scope of the project analysed to ensure time on site is being used for the best outcome. The work on a larger building, due to its complexity often over several floors or even adjoining buildings, sometimes means it has to be done outside of normal operating hours to allow site work to continue uninterrupted.
Commonly a pre-test site visit or visits will be done to walk the test building so that potential issues can be identified with the air tightness champion both from plans and though a detailed visual inspection. This will identify not only weak points to be remediated in advance of the test but also what pre test works are to be completed by the building contractor. This cooperation saves both time when testing and reduces to a minimum the potential for a poor test outcome.
The skills and equipment used can also be applied to other specialised types of testing such as Clean Room Testing and the testing of Fire Suppression Systems
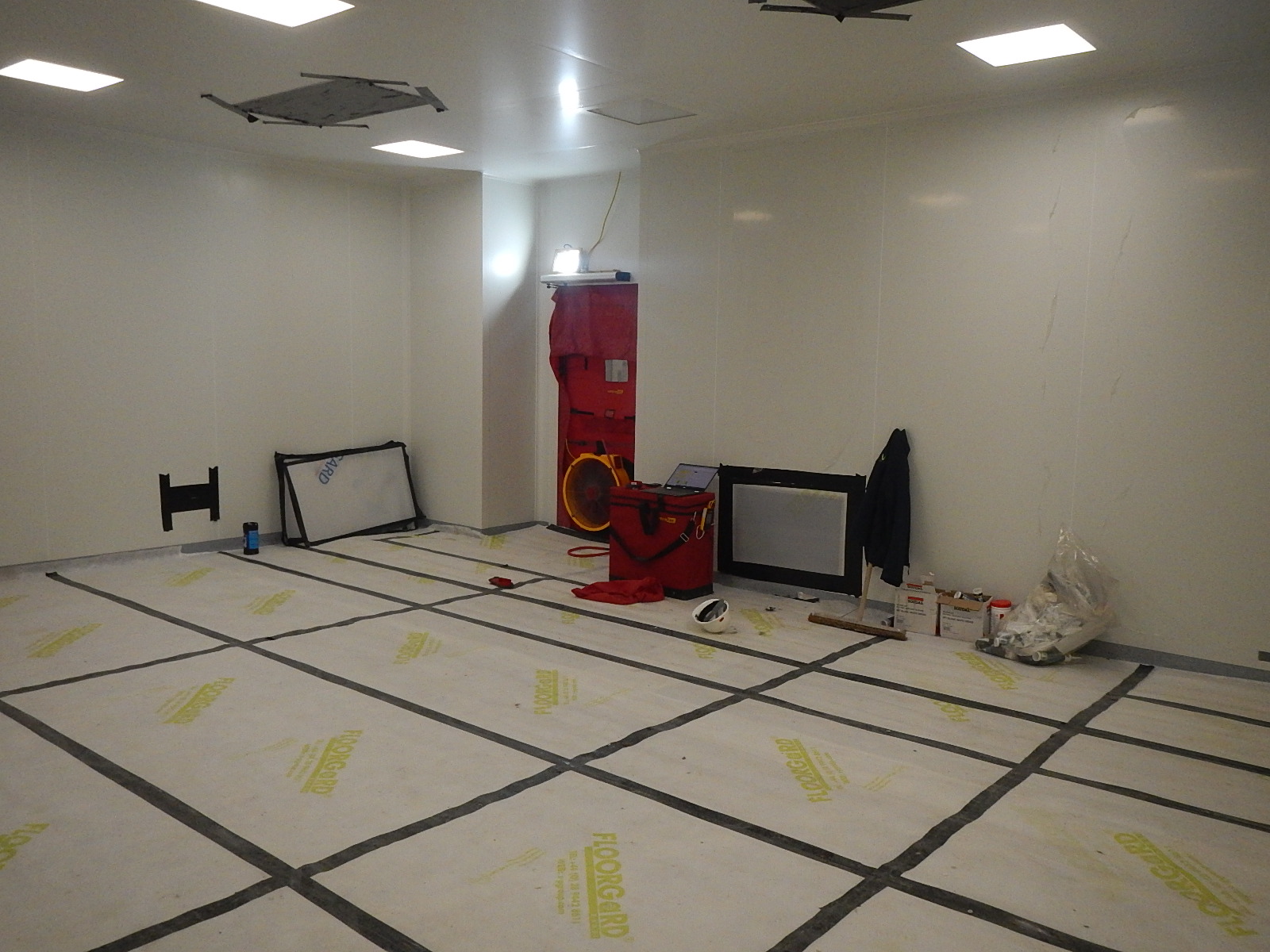
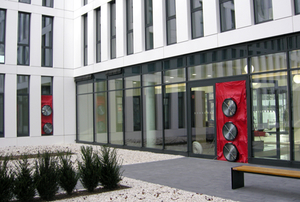
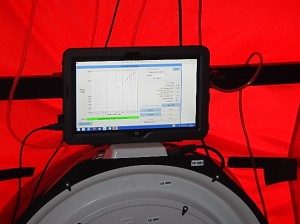